How can condition monitoring reduce downtime in the mining and quarrying industry?
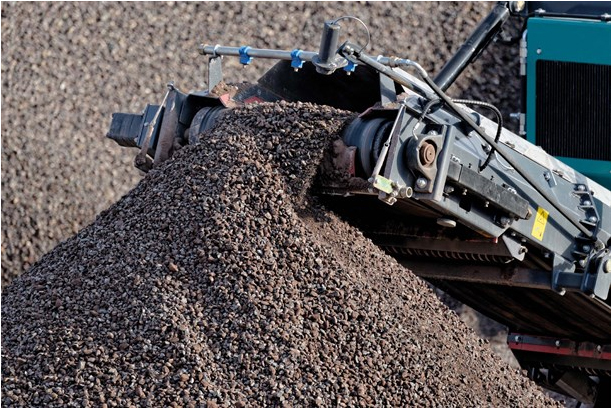
In the harsh, highly contaminated environments of the mining and quarrying industry, downtime has come to be expected and almost accepted as standard. Many users over-maintain equipment, replacing bearings more often than necessary, in an attempt to try and reduce the chance of failure. However, catastrophic failures still occur without any warning, even in the highest quality equipment, leading to costly downtime and expensive repair bills. This doesn’t have to be the case.
A catastrophic machine failure in the aggregates industry can result in hours or even days of unplanned downtime, costing thousands of pounds in lost revenue. It also creates the potential for serious injury, both as a direct result of the failure and during the repair, with workers 28% more likely to have an accident performing reactive maintenance over planned maintenance.
Condition monitoring is a method of proactively monitoring the state of machine components, to be able to identify areas of potential failure before the failure occurs. Preventative maintenance can then be scheduled during planned shutdown times, avoiding costly unplanned downtime.
An excellent condition monitoring solution for the aggregates industry is the SKF Copperhead Fault
Detection System. The system comprises of the Copperhead Transmitter Unit (CMPT CTU), the Alarm and Display Module (CMPT DCL) and Copperhead (CMPT) Sensors. It has the potential to continuously monitor up to 16 bearings in both low and normal speed applications, ensuring that vibration, temperature, speed and load are within specified parameters. Little training is required to operate the system, and it can be used as a stand-alone device, or integrated into a plant automation system.
Despite the surrounding noise and vibrations, Copperhead is a means of offering a safeguard for measuring the condition of bearings, grease, overall machinery and structural vibration; indeed most general machine faults. It can detect looseness, misalignment and unbalance. It can be used to identify repetitive impact-type vibrations generated by rolling bearing damage, machinery faults due to loose components, gear faults and lack of lubrication.
Benefits of the Copperhead Fault Detection System include:
- Increased machine reliability
- Extended maintenance intervals
- Reduced costs
- Increased productivity
- Enhanced operator safety
- Reduced environmental impact
A common misconception is that condition monitoring systems are expensive. The initial outlay often puts people off, but the reality is that just one early fault detection can offset the cost of a predictive maintenance programme, as well as improving site safety and providing peace of mind. If the average cost per hour of a machine is taken at £1500, and it takes four hours to replace a broken unit and clear the remaining debris, the unit has more than paid for itself in just one instance.
The conditions associated with the aggregates industry are always going to be challenging, but systems like Copperhead can reduce the likelihood of catastrophic failure, increasing reliability, reducing downtime and improving site safety. What’s stopping you from making the change?
Clive Simkins is Acorn’s bearings and maintenance product manager. With over 18 years’ experience in the industry, working alongside distributors, engineers and buyers, he has the technical expertise to find the perfect solution for any application.