5 ways to prevent premature bearing failure
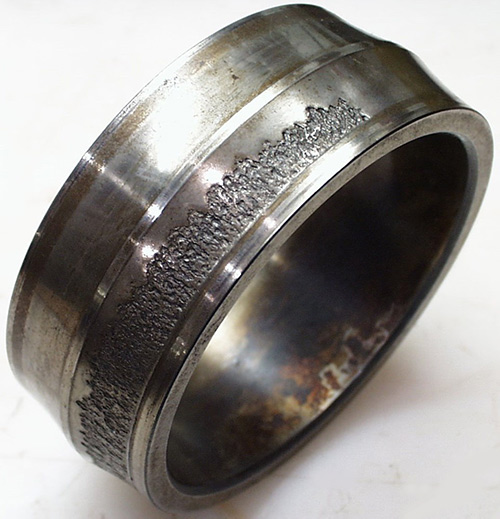
From costly downtime to catastrophic machine failure: everyone knows the potential consequences of premature bearing failure. At ACORN, we want to help you avoid this, keeping your production moving and helping you to save on costs.
Find out more about the consequences of bearing failure
We’ve put together a list of the five easy steps that you can take to help to prevent the most common causes of bearing failure in your machinery.
1. Bearing selection
Let’s start from the beginning: bearing selection. If the incorrect bearing is selected for an application, the chances of bearing damage are high.
When selecting a bearing, take into account the operating conditions, operating environment, amount and direction of load, operating speed and any misalignment that the application is subjected to. Re-evaluate the bearing selection if there are any changes to these operating conditions to ensure that the bearing you have chosen is still suitable.
If you’re in any doubt about which type of bearing will be most suitable for your application, contact your local branch who will be happy to help.
2. Lubrication
Using too much or too little lubricant can be extremely detrimental to a bearing, with around 36% of premature bearing failures attributed to poor lubrication. It’s also essential to ensure that the lubrication is suitable for the operating conditions and environment as harsh conditions such as high temperatures may cause lubricants to degrade if they aren’t of a suitable type.
Follow the bearing manufacturer’s guidelines for lubrication quantity and intervals. For extra accuracy, automatic lubricators can be fitted to ensure that exactly the right amount of lubricant is delivered to the bearing at the correct interval.
3. Seals
Seals are important for protecting the bearing from external contamination, as well as retaining the lubricant within the bearing. If a seal isn’t operating effectively, or if it loses contact as a result of a high pressured washdown, it may allow contamination to enter the bearing, causing the bearing to fail prematurely.
The seal needs to be suitable for the operating environment, including any contamination or cleaning processes that the application may be subjected to. It’s also important to ensure that the seal is appropriate for the operating temperature of the application, as high temperatures may cause seals to become brittle over time.
4. Fitting
Fitting methods such as the use of brute force or unstable heat sources such as naked flames often cause bearing damage through weakening of the internal structure.
The key here is to use the right fitting technique for the bearing. This could be controlled force, bearing heaters or a bearing fitting toolkit. If you aren’t sure, the best thing to do is to seek advice from a bearing expert.
5. Condition monitoring
All too often, engineers don’t know about a problem until the point of failure. This leads to downtime whilst replacement parts are sourced and repairs are carried out. What if there was a way to predict the failure before it actually occurs?
Condition monitoring systems monitor conditions such as the temperature and vibration levels of a machine, alerting the user if the readings deviate outside of the usual parameters. This allows repairs to be planned into preventative maintenance to avoid the bearing failure, rather than causing downtime when the failure occurs.
Although premature bearing failure is difficult to eradicate completely, there are measures you can put in place to reduce the risk, and to detect problems before they turn into failures.
To find out more about how you can extend the life of your bearings, or for a personalised consultation for your machinery, contact your local sales team today.