5 ways to improve the efficiency of your electric motor
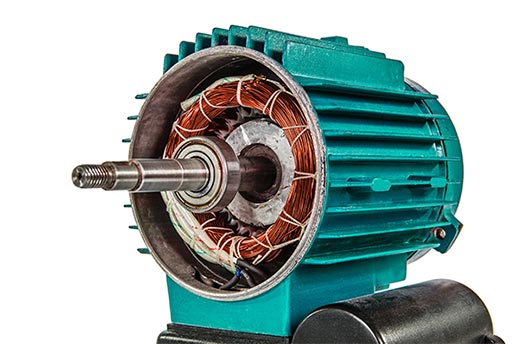
Electric motors are found in almost every application, across every industry. They are the driving force of most machines, and need to be able to stand up to whatever is thrown at them. Electric motor failure can bring an entire plant to a standstill, causing hours or even days of unplanned downtime, resulting in high cost to the business.
Improving the efficiency of your electric motor can reduce the likelihood of machine failure, extend component lifespan and help to reduce energy consumption.
Here are our top five tips to improve the efficiency of your electric motor:
1. Regular inspection
The most common cause of motor failure is low resistance. This occurs when the insulation of the windings is degraded, by adverse conditions such as overheating, corrosion or physical damage, leading to insufficient isolation between windings, leakages, short circuits and eventually motor failure.
Regular inspection of the insulation for signs of wear can help to keep your electric motor running at full efficiency and prevent low resistance from resulting in machine failure.
2. Protect against electrical overload
Electrical overload or over-current occurs when the current that the motor is designed to carry efficiently and safely is exceeded. The most common cause of this is a low voltage supply, which causes the motor to draw in extra current in an attempt to maintain torque. However, it can also be caused by short circuited conductors, or an excessive voltage supply.
The installation of effective over-current protection can detect over-current before it becomes a problem, interrupting supply and protecting against overload. This will enable the motor to operate at maximum efficiency, whilst reducing the chance of breakdown.
3. Keep cool
With around 55% of insulating motor failures caused by overheating, the benefits of keeping your motor cool are clear to see. For every 10 degrees celcius that the temperature of a motor is raised, the insulation life is reduced by 50%.
Ensuring that the operating environment is kept cool is the easiest way to keep the temperature of a motor down. This will help to prevent breakdowns, increasing the efficiency of your electric motor.
4. Monitor vibration
Vibration in electric motors is commonly caused by an uneven or unstable surface. However, it can also be a result of an underlying problem such as loose bearings, corrosion or misalignment. It’s important to monitor vibration levels, as excess vibration can cause the motor to fail prematurely.
A motor analysing tool such as SKF’s Enlight QuickCollect: a simple, low cost option which is ideal for monitoring the vibration level and temperature of an electric motor. This can help to ensure that the motor is able to run at full efficiency and reduce the risk of premature motor failure.
5. Protect against contamination
Electric motors often operate in environments which are contaminated by dust, dirt or chemicals. However, with contamination being one of the leading causes of motor failure, it is critical to ensure that electric motors are well protected against contamination.
Keeping work areas, tools and fixtures as clean as possible can reduce the chance of contamination coming into contact with the motor. It’s also helpful, wherever possible, to position motors away from grinding machines and other equipment which produces large amounts of contamination. This will reduce the opportunity for contamination to enter the motor, keeping efficiency at the highest possible level and reducing the likelihood of machine breakdown.
For more information about how you can improve the efficiency of your electric motor, contact our dedicated couplings & drives division today.