8 coupling mistakes that could cost you
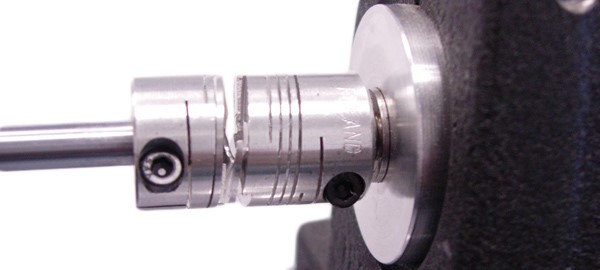
It’s no secret that every business wants to keep costs to a minimum in order to maximise profit. Unfortunately, machine breakdowns often happen unexpectedly, causing unplanned downtime and expensive repair bills.
Couplings are often viewed as simple components which do not require much consideration or maintenance. However, a coupling failure can be catastrophic, causing hours or even days of unplanned downtime and significantly impacting on profit.
In this article, we look at the eight most common coupling mistakes which could cost your business.
1. Choosing the wrong coupling
One of the most expensive coupling mistakes you can make is to select the wrong coupling for your machinery. It’s important to consider torque, RPM, operating conditions, shaft size, tolerances and misalignment when choosing the right coupling for your application.
2. Missing misalignment
Misalignment can cause stress to a wide range of machine components, including couplings and bearings. If misalignment is identified in the application, an appropriate coupling can be selected which can accommodate this misalignment, helping to protect connected components and prevent premature failure.
3. Improper installation
It is important to follow manufacturer installation instructions when fitting a coupling. Incorrect installation of a coupling can lead to premature wear of system components and premature failure of the coupling. Improper installation can range from uneven torqueing of the screws to installing off-centre.
4. Exceeding recommended RPM
Every coupling has its own RPM rating, which must not be exceeded. Exceeding the manufacturer’s RPM rating can cause damage to machine components and ultimately coupling failure. It’s important to ensure that the application’s maximum RPM will not exceed the coupling’s RPM rating during the design process in order to avoid costly breakdowns.
5. Not considering coupling wear
In most applications, couplings are the element of wear, protecting critical components such as bearings and motors. Different types of couplings will wear in different ways, with different types of failure. For example, beam and bellows couplings will stop power transmission when they fail, whereas disc, jaw and Oldham couplings will continue to transmit power but lose their zero-backlash capabilities. The application requirements will dictate which type of coupling is required.
A maintenance schedule can be put in place to replace the coupling or wear element before the point of failure to avoid costly system damage or unplanned downtime.
6. Failure to test
When designing a new application, it is important to test components before the system goes live. Everything may appear correct in the design but suitability cannot be confirmed until the coupling is running under the exact operating conditions.
7. Buying generic couplings
Generic couplings may appear identical to premium brands in terms of specifications, tolerances and designs, but the quality is generally inferior. These couplings may be suitable for applications which have low performance requirements, but they are unlikely to offer the levels of performance required for precision systems.
Purchasing couplings from a respected manufacturer provides you with the reassurance that your coupling can stand up to the high performance standards that you expect, minimising downtime and costs to your business.
8. Leaving coupling selection too late
A common mistake is to select couplings late in the design process. This can limit which coupling can be used in the system, along with the performance that it can deliver. Selecting a coupling early in the design process means that you can ensure there is enough space for the most appropriate coupling for the application. This helps to save time and money, as well as ensuring performance.
For help selecting the right coupling for your application, contact our dedicated couplings and drives division today.