Extending maintenance intervals in the mining and quarrying industry
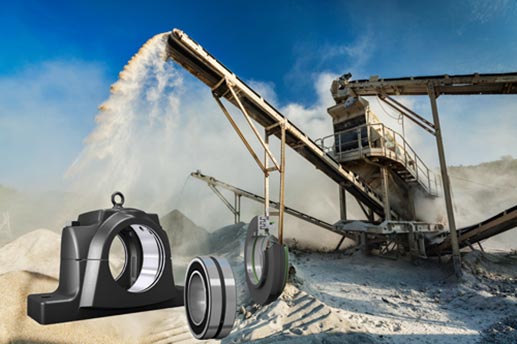
Conditions are harsh in the mining and quarrying industry and it is well known that machinery operating in these arduous conditions is often subject to frequent breakdown. This results in extensive downtime for the plant, leading to a reduction in profits.
Conveyor pulleys are no different. They operate under heavy loads whilst their open bearings are exposed to high levels of contamination and subjected to high-pressure washdowns. The ingress of dirt into the bearing leads to indentations in the bearing raceways, whilst the washdowns cause grease to be lost, with insufficient lubrication remaining within the bearing.
The harsh conditions which conveyor pulleys are exposed to result in frequent conveyor breakdowns and high maintenance requirements. In the majority of mining plants, conveyor availability is under 87%, meaning that profit margins are severely restricted.
The SKF Three-barrier solution features the new SKF Taconite sealing with two rings – one stationary and one rotating. This forms a narrow labyrinth between the two rings. Bolt-on end covers provide further protection against contamination and lubricant leakage. This solution was designed to extend the service life of bearings such as those used in conveyor pulleys, reducing downtime and extending maintenance intervals.
Replacing an open conveyor pulley bearing with the SKF Three-barrier solution can increase availability to up to 92%. This is due to the SKF Three-barrier solution having an average lifespan which is three times longer than an open bearing.
This sealing solution can be combined with an SKF Mining Specification variant housing, providing exceptional levels of durability and reliability, even in the harsh operating conditions of the mining and quarrying industry.
The innovative design of the SKF Three-barrier solution means that re-greasing only needs to be completed twice a year, in comparison to the weekly greasing of open bearings. This reduces the time spent on maintenance by up to 90%, reducing both costs to the business and downtime.
These reduced maintenance requirements and increase in mean time between failure means that worker safety is also greatly improved, as maintenance can be scheduled rather than performed reactively. With workers 28% more likely to have an accident performing reactive maintenance rather than proactive maintenance, this represents a vast improvement in worker safety.
This bearing solution is also ideal for businesses who are looking to improve their sustainability, as up to 90% less grease is required. This helps to keep wastage to a minimum, as well as keeping costs down.
To find out more about the SKF Three-barrier solution and how it could work for your business, contact your local team of experts today.