The ACORN Bearing Compendium: Why do Bearings Fail? Part 6
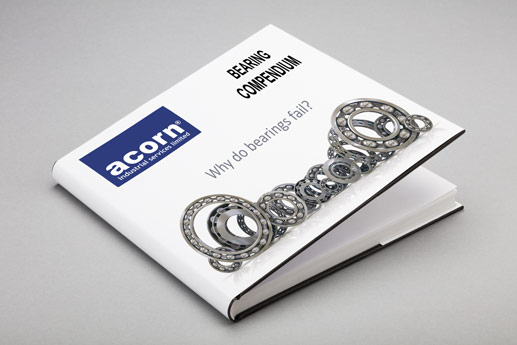
Bearing failure is one of the most common causes of machine downtime. And let's face it, no matter what industry you're in, downtime isn't just an inconvenience - it's also costly. To reduce your machine downtime, you need to understand why bearings fail and how you can prevent this from happening.
So, why do bearings fail? To answer this question, you need to understand the most common causes of bearing failure. However, it's also important that you know how to prevent each of these causes of failure from happening. After all, prevention is the best cure.
In this article, we'll go through the top five causes of bearing failure, as well as explaining how you can keep your bearings in the best possible health, helping you to avoid bearing failure and the consequent downtime that it causes.
1. Incorrect lubrication
Poor lubrication is the most common cause of bearing failure, and knowing how to care for your bearings can make a huge difference when it comes to avoiding bearing failure caused by improper lubrication.
There are a few different ways in which bearing failure can result from lubrication:
- Insufficient lubrication - if your bearing does not have enough lubricant, or you do not apply lubricant often enough, it could run hot and eventually seize. This is because bearings rely on a certain amount of oil in order to perform effectively. If there isn't enough oil in your bearing, it can seize - causing dangerous conditions and leading to costly downtime for your machine.
- Over-lubrication - over-lubricating your bearing can also cause problems. It seems counter-intuitive, but excess lubrication can cause leakage through the bearing's seal. This can cause the seal to become compromised, allowing the ingress of contamination into the bearing and leading to its ultimate failure.
- Wrong type of lubricant - There are many different types of lubrication on the market, from oils to greases. It's essential that you choose the correct type of lubricant for your operating conditions, or you could risk compromising your bearing. For example, if the bearing is located within an oven, you will need to choose a grease or oil that is designed to withstand high temperatures.
The best way to ensure that your bearing doesn't become a victim of improper lubrication is to consult with an expert in bearing maintenance to ensure that your choice of lubrication and your maintenance schedule is optimum for your machinery and your operating environment. This will help you to ensure that your bearings are receiving the care that they need to achieve a long and productive service life.
2. Contamination
If your bearing becomes contaminated, this could lead to premature bearing failure. There are a few ways in which your bearing could become contaminated:
- Incorrect seal - One of the most common reasons for a bearing becoming contaminated is an incorrect seal being used. It could be that your seal isn't sufficient for the levels of contamination being experienced, or that it isn't suitable for the speed, temperature or load of the application.
- Poorly fitted seal - If a seal doesn't fit properly, there will be a small gap that allows the ingress of contamination into the bearing.
- Degradation of seal - When a seal becomes old, or if it becomes compromised as a result of extreme temperatures or abrasive contamination, it may begin to degrade. This could enable contamination to enter the bearing, eventually leading to premature bearing failure.
- Improper storage - Bearings should be stored according to the manufacturer instructions. This usually means leaving the bearing in its original packaging in a cool and dark location until the point of fitting. If the bearing is not stored correctly, it could become contaminated before it is even mounted to the application.
- Improper handling - It's important that bearings are handled carefully during the mounting process, with due care taken to avoid any contamination entering the bearing. It is also essential that the equipment used for mounting the bearing has been thoroughly cleaned to prevent contamination.
The best way to avoid your bearing failing as a result of contamination is to follow the manufacturer's instructions carefully when it comes to storing the bearing, and to handle it carefully during the mounting process to avoid any potential contamination.
It's also essential that the bearing is fitted with an appropriate seal, taking into account the operating environment, as well as the running conditions of the machinery. The seal should be inspected at regular intervals to ensure that it fits the bearing properly and has not begun to degrade.
3. Fatigue
According to SKF, around 34% of all premature bearing failures can be attributed to fatigue. This makes fatigue the leading cause of premature bearing failure. Whilst bearings can fail due to fatigue at the end of their natural lifecycle, bearing fatigue is more commonly the result of the wrong bearing being specified for the application.
This does not necessarily mean that the wrong bearing was selected during the specification process. It's common for the operating characteristics of machinery to change over time. This is often the result of higher levels of demand being placed on the machinery, requiring it to operate at higher speeds or with heavier loads. However, this places additional demands on machine components, including the bearings.
It's vital that you take into consideration both the running characteristics and the operating environment of the machinery when specifying a bearing. However, it's also critical that bearing suitability is reconsidered whenever there is a change to the operating conditions. This could be a change in speed or load, or it could be a change in the external operating environment, such as the temperature or levels of contamination.
Ensuring that you have chosen the right bearing for your application, and continuing to reassess this at regular intervals, will help to reduce the risk of bearing failure as a result of fatigue.
4. Incorrect mounting
Approximately one sixth of all premature bearing failures are the result of incorrect mounting practices. This is because bearings commonly become damaged during the fitting process, causing them to fail prematurely.
There are three different ways in which a bearing can be safely fitted:
- Mechanical - using a bearing fitting toolkit
- Heat - using a bearing heater
- Oil - using oil injection techniques
Mechanical fitting methods can be both safe and effective if done correctly. This means using a bearing fitting toolkit such as SKF's TMFT 36 to ensure that force is applied evenly across the bearing and that damage does not occur during the mounting process.
Brute force is often used when fitting bearings. However, this frequently leads to force being applied unevenly to the bearing, resulting in damage occurring. Although you may not notice this damage during the mounting process, this damage could lead to the bearing's premature failure later down the line.
Heat is a highly effective method for mounting bearings. However, bearings should be heated using a bearing heater, rather than a naked flame or oil bath. This is because the bearing is often heated unevenly when a naked flame or oil bath are used, leading the bearing to become damaged during the fitting process. Flames and oil baths can also lead to severe injuries for the engineers involved.
Selecting an appropriate mounting method for your bearing can help to prevent any damage being inflicted on the bearing that might later cause its premature failure, as well as helping to keep your workers safe.
5. Improper handling
When you're handling bearings, it's essential that you take proper precautions. This is because the handling process is a time where the bearing is at high risk of damage, through scratches or indentation.
It's also essential that you store your bearing according to the manufacturer's instructions. This typically means keeping your bearing in its original packaging in a cool, dark room until you are ready to fit it to your machinery.
When your bearing is being stored and handled, it is at its highest risk for being exposed to contaminants such as dust or dampness. If due care is not taken, it could also risk being damaged by being knocked or dropped. This could lead to the bearing failing prematurely due to damage sustained or contamination that has entered the bearing.
Properly storing your bearing and ensuring that it is handled carefully at all times will help it to achieve its full service life, avoiding premature failure as a result of improper handling or storage.
How to avoid bearing failure
Whilst bearings will inevitably fail at the end of their service life, premature bearing failure is unfortunately a common occurrence that can be prevented with the right knowledge.
To give your bearings the best chance of achieving their full service life, there are a few steps that you can follow:
- Ensure that you specify the correct bearing for your application requirements as well as the environment in which it operates.
- Regularly check that you're still using the most appropriate bearing for the operating conditions.
- Use a safe and effective method for mounting your bearing, such as using a bearing fitting toolkit or a bearing heater.
- Store and handle your bearings carefully, in accordance to the manufacturer's instructions.
- Ensure that you are using the most appropriate sealing solution for your application, and regularly inspect the seal for signs of degradation or misalignment.
- Check that you are using the most appropriate lubricant for the application, as well as the operating environment.
- Regularly inspect the bearing for any signs of wear or damage. If the bearing appears damaged, replace it at the soonest opportunity to avoid catastrophic failure.
- When a bearing fails prematurely, inspect it for any visible damage and consider sending it to a bearing expert for root cause analysis. Of course, you can’t save the bearing after it has failed but finding out the cause of the problem could help you to avoid future failures and downtime.
In summary
Premature bearing failure is a common problem in industry, but the majority of the time it can be prevented by following the tips above. If you're unsure of how to keep your bearings operating at their best, it's best to seek advice from a bearing expert. They will be best placed to offer advice on maintaining your bearings and reducing your risk of premature bearing failure.
In this article, we have answered the question 'why do bearings fail', as well as explaining how you can use your new knowledge to prevent your bearings from failing prematurely. For more assistance in getting the most out of your bearings, contact your local ACORN branch today.