Top 5 reasons for seal failure (and how to prevent them)
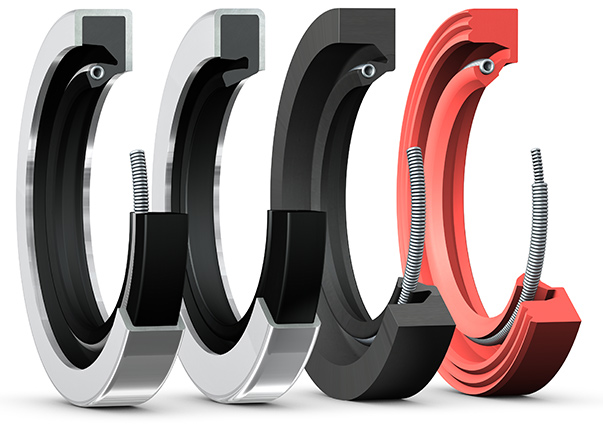
Bearing seals are perhaps one of the most underrated components on any machine. They perform the essential role of guarding against contamination whilst keeping hold of the lubricant. When a seal fails, it is often quickly followed by bearing failure: a costly consequence.
By understanding the causes of seal failure, we can put measures in place to prevent it, extending machine life.
Reason 1: Incorrect seal used for operating conditions
Problem: Operating conditions such as extreme temperatures and chemical environments can be extremely damaging to seals if they are not designed for the challenging environment, which commonly results in the premature failure of the seal.
Solution: During the seal selection process, consider the normal operating conditions of the application, as well as auxiliary activities such as cleaning regimes. Any change in the operating parameters of the application, such as speed, temperature or environment, should result in a further assessment of the sealing capabilities of the application to ensure that the seals in operation are still optimal.
Reason 2: Improper fitting practices
Problem: Improper fitting practices such as the use of brute force or excessive heating can cause irreparable seal damage.
Solution: Follow manufacturer guidelines carefully during storage and fitting. Using a bearing heater can help to ensure that excess heat is not applied. Fitting toolkits such as the SKF TMMK series are ideal for fitting and removing bearings without causing seal damage.
Reason 3: Misalignment
Problem: Shaft misalignment can cause the seal to be pushed to one side and lose sufficient contact with the shaft, allowing the ingress of contamination into the bearing.
Solution: Visual signs of shaft misalignment, such as the leakage of lubricant through the seal, are often the first indication of a problem. An elevated running temperature of the bearing can also indicate a problem with misalignment which could cause seal failure. Shaft alignment should be checked every time maintenance is performed on the machine, using a laser alignment tool such as the SKF TKSA series.
Reason 4: Excessive lubrication applied through seal
Problem: It can be tempting to apply just a little bit extra lubricant to extend the relubrication interval and guarantee that the lubricant won’t run out. However, overloading your bearing with lubricant can do more harm than good, when the lubricant uses the weakest point in the bearing, or an external seal, to escape. This can cause irreversible seal damage, allowing contaminants to enter the bearing and resulting in premature bearing failure.
Solution: To avoid seal damage by excess lubrication, ensure that you use a controlled and measured method of lubricant application. This could be an automatic lubrication system, such as SKF System 24, or a manual lubrication tool such as a grease gun with a grease meter. Ensure that you always follow manufacturer guidelines for the frequency and quantity of lubricant application to prevent overloading.
Reason 5: Contamination as a result of high pressure washdowns
Problem: High pressure washdowns which are common in the food & beverage and pharmaceuticals industry may damage seals and allow the ingress of contamination into the bearing.
Solution: Specialist bearings are available, for example SKF Food Line housed units, which are designed to withstand the high pressure washdowns which are common in these industries.
If you have a problem with seal failure on your application, why not contact your local sales team who can offer expert guidance to help you to find a solution.
You may also be interested in:
How do you tell if you've got a top quality Freudenberg radial shaft seal?