When reliability meets sustainability: Aligning sustainability targets with food safety
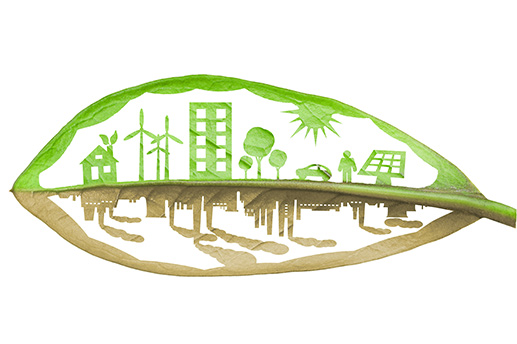
Sustainability has become the buzzword of the 21st century and that is set to continue for the foreseeable future. However, it’s not always easy to prioritise sustainability in the midst of increasingly challenging cost, output and food safety targets.
What if you could demonstrate tangible environmental benefits whilst enhancing the reliability and food safety of your plant?
In this article, we’ll explain how you can drive down your downtime, prioritise food safety and deliver incremental environmental benefits, proving that you really can have it all.
Reduce your environmental impact with re-lubrication free bearings
One of the most effective ways to reduce your environmental impact and optimise your food safety is to upgrade to re-lubrication free bearings. The benefits are far-reaching, from the reduced cost of lubricant and component replacements, to the elimination of wastewater contamination from washed-down bearings grease.
Cut water usage and environmental waste
Every plant manager will know how important it is to have food grade components on your production line. Not only are SKF’s Food Line bearing units food grade, but they can also reduce your water consumption by 33% whilst generating zero landfill.
SKF Food Line ball bearing units are completely sealed, lubricated for life, and designed for optimum performance in even the harshest of processing and cleaning environments.
Lubricate bearings with fryer oil
Fryers present a challenge to many plant managers, with bearings often failing prematurely and high levels of maintenance required. What if we told you that you could use the operating conditions to your advantage?
SKF Fryer Bearing Units allow the cooking oil to enter the bearing, acting as an effective lubricant. This enables bearings to run for up to 16,000 hours, eliminating the need to relubricate the bearings after each caustic boil out. You’ll benefit from a significant reduction in maintenance, enhanced uptime and increase reliability, whilst your carbon footprint is reduced.
Reduce the footprint of high temperature greased bearings
High temperatures can lead to your bearings failing to achieve their expected service life. Not only will this affect the uptime and productivity of your production line, but it also leads to additional waste and an increased carbon footprint.
SKF high temperature bearings eliminate the need to re-lubricate, in even the highest temperature applications. The fully crowned pure graphite cage allows just enough contact between the balls and cage to create a fine powder which coats the rolling elements to eliminate metal-to-metal contact. This enables production lines to minimise their environmental impact whilst reducing maintenance expenditure.
Prevent corrosion in challenging conditions
When you’re dealing with freezer applications, you’ll be trying to counter the effects of high levels of humidity and rapid temperature changes. This can take its toll on even the highest quality of bearings.
SKF bearings with Solid Oil technology are designed to stand up to challenging environments, such as within freezer applications. Available with NSF H1 approved food-grade lubricant, these bearings do not require relubrication throughout their service life. This helps to maximise reliability and reduce costs, whilst ensuring food safety.
Cut your costs whilst prioritising sustainability
Traditional conveyors utilise a huge quantity of water and lubricant every single day during operation. This creates a large amount of wastage, as well as attracting a high cost to the business.
The SKF Dry Lubrication System for Conveyors offers a practical solution which cuts maintenance requirements whilst prioritising sustainability. This fully automated system applies a small amount of SKF Dry Film Lubricant to conveyor chains and guides, keeping the line moving at all times.
Not only does this cut costs and reduce both water and lubricant consumption, but it also helps to improve operator safety, reduce clean-up costs, and optimise productivity.
ACORN: Your sustainability partner
In today’s modern world, every business needs to prioritise sustainability, ensuring environmentally friendly operation at every stage of the production process.
However, we understand that it isn’t always easy to balance your sustainability goals with other operational targets, such as cost, uptime and food safety. We’re here to help you.
Our experts can help you to meet your operational goals, without having to compromise on sustainability. Simply give us a call and we can arrange a site visit to identify your pain points and offer solutions that really work for your business.