5 Tips for Spherical Roller Bearing Maintenance
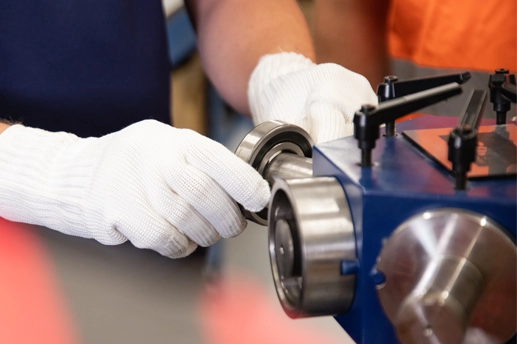
If you want your spherical roller bearings (opens new window) to perform at their best, and last, then proper maintenance isn’t just optional, it’s essential.
Whether you’re dealing with heavy loads, misalignment, or contaminated environments, taking a few proactive steps can go a long way in extending the life of your bearings.
1. Handling & Storage
You may not realise it, but how you handle and store your bearings can directly affect their performance and longevity.
Always keep bearings in their original, unopened packaging until you’re ready to use them. This packaging provides a barrier against contaminants and moisture that can cause corrosion or early failure. Bearings should be stored in dry area that isn’t subject to extreme temperatures or humidity.
When you’re ready to mount the bearing, timing and cleanliness matter. Remove it from the packaging only when you’re set to install it, not before. Always handle with clean, dry hands or lint-free cloths. Don’t set components down on dirty benches or workshop floors.
Remember: contamination kills bearings.
2. Mounting & Fitting
Poor mounting practices are one of the top reasons bearings fail early. Data from SKF Bearing Life Cycle (opens new window) shows that around 16% of premature bearing failures are down to incorrect fitting. That’s why it’s worth getting it right.
Firstly, keep the fitting environment clean and controlled. If you’re working in a dusty or heavily contaminated area, keep the bearing wrapped until the last possible moment. For smaller spherical roller bearings, use tools like the SKF TMFT 36 (opens new window) fitting kit to distribute forces evenly during mounting.
For larger bearings, it’s best to apply heat to expand the inner ring before mounting. SKF induction heaters (opens new window) are ideal for this, with models suitable for bearings up to 120kg or more. It is particularly important for sealed bearings that you make sure not to overheat the bearing. Most sealed spherical bearings should be heated to a maximum of 80°c, or up to the lower permissible limit of the seal or grease being used.
Adapter sleeves (opens new window) can also make mounting easier and more secure, particularly on stepped shafts, giving you a reliable and concentric fit without the need for excessive force.
3. Lubrication
To operate reliably, rolling bearings require adequate lubrication. It minimises wear, reduces friction, and protects against corrosion. But the right lubricant at the correct quantities makes all the difference.
Select a high quality grease or oil that suits your specific application and operating conditions, then stick to a regular lubrication schedule, or set up an automatic lubricator and check back. Too little and the bearing wears out early; too much and you risk overheating or seal damage. For example if your spherical roller bearings are working with high loads and temperatures, you may opt for a high performance grease such as the SKF LGHB2 (opens new window) grease.
Make sure to check lubricant levels and top up or replace as needed. Over time, even the best grease breaks down and loses effectiveness.
4. Sealing
Seals (opens new window) can be one of the simplest, most cost-effective ways to boost bearing life, especially in environments where dust, water or chemicals are an issue.
A good seal keeps lubrication in and contamination out. That means less maintenance, fewer breakdowns and a more reliable bearing.
Make sure you are picking the best seal for the job and keep checking their integrity throughout the bearing life. In high-speed or high-temperature applications, the wrong seal can do more harm than good. Always check the material, temperature range, and design when selecting a seal for your spherical roller bearing.
5. Operating conditions
Even a perfectly installed, well-lubricated bearing can fail if it’s running in the wrong conditions. Keep an eye on temperature, load, speed and vibration levels. These factors can drift over time, and even slight changes can shorten bearing life significantly.
Use monitoring tools like infrared thermometers, tachometers, stroboscopes and mechanical stethoscopes to stay ahead of potential issues. Regular condition monitoring gives you a window into your machine’s health, letting you catch problems before they turn into expensive downtime.
Conclusion
Spherical roller bearings are designed to work hard, but the need the right maintenance to reach their full potential. From proper storage and careful handling, through to correct mounting, effective lubrication, and ongoing condition monitoring, each step of the bearing’s life cycle matters. Getting maintenance right will help maximise performance, minimise downtime, and get the most out of your bearings.
Talk to our Bearing Product Expert (opens new window) today about your bearing maintenance plans.