The ACORN Bearing Compendium: Bearing Terminology, Part 2
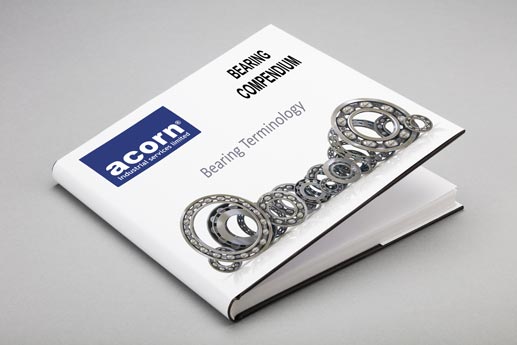
Most people will have heard of a bearing, but do you know what a bearing cage, rolling element or a raceway is? How about the difference between dynamic and static load?
The world of bearings is complex, with lots of technical jargon thrown around. We’ve put together some of the most commonly used bearing terminology to help you to understand what you’re talking about when it comes to bearings.
ABEC
ABEC stands for ‘Annual Bearing Engineering Committee’ and is used as a standard for measuring bearing precision. You’ll typically see this acronym preceding a number which specifies a particular degree of precision. The higher the number, the higher the level of precision the bearing has.
A standard ball bearing will typically have a precision rating of ABEC 1. ABEC 3 signifies precision, ABEC 5 is high precision and ABEC 7 is extremely high precision. Simply put, the higher the level of precision, the closer the bearing is manufactured to its specified sizes.
Accuracy
Accuracy describes the precision to which the bearing is manufactured to the specified dimensions. Whilst all bearings are highly precise components, some are manufactured to higher levels of accuracy than others.
Generally speaking, the higher the level of accuracy, the better the performance of the bearing as noise and vibration will be reduced and the starting and running torque will be increased.
For many applications, accuracy is not a significant consideration. However, certain applications such as machine tool spindles, high-speed rolling mills, vacuum pumps and balancing machines demand the highest possible levels of accuracy.
Adapter sleeve
Adapter sleeves are the most commonly used components to locate a tapered-bore bearing onto a shaft. This is due to their ease of installation and accurate fit on the shaft which helps to prolong bearing life.
Adapter sleeves are suitable for use on both plain shafts and stepped shafts. On a plain shaft, an adapter sleeve allows the bearing to be located at any point along the shaft. On a stepped shaft, the bearing can be accurately positioned axially, facilitating the mounting and dismounting of the bearing.
Angular contact ball bearing
Angular contact ball bearings feature inner and outer ring raceways which are displaced relative to each other in the direction of the bearing axis. This gives angular contact ball bearings the ability to accommodate both radial and axial loads simultaneously, making them ideal for applications which require combined load carrying capacity.
Angular contact ball bearings can typically accommodate axial load in only one direction. If you require axial load capacity in both directions, you can choose to mount a pair of angular contact ball bearings, or you can choose to use a double row angular contact ball bearing which can accommodate axial load in both directions.
These bearings are commonly found in demanding applications such as pumps, compressors, gearboxes and machine tool spindles.
Axial (thrust) load
Axial load is transmitted along the axis, parallel to the shaft. This type of load is also known as thrust load. This is often the case in industrial fans, pumps and transmission applications.
The majority of bearings are designed primarily to facilitate radial load. However, there are some bearings on the market which are designed specifically to carry axial load. These include needle roller thrust bearings and thrust ball bearings.
When axial load occurs alongside radial load, this is known as a combined load. Bearings such as angular contact ball bearings and tapered roller bearings are designed to accommodate combined loads.
Ball bearing
Ball bearings consist of metal balls which are held together by a cage or retainer. These are situated between two races known as the inner and outer rings. The metal balls separate the bearing races, reducing rotational friction whilst supporting radial load.
Ball bearings are typically able to operate at high speeds whilst tolerating a small amount of misalignment. However, due to the smaller contact area between the balls and races, ball bearings generally have a lower load carrying capacity than their roller bearing counterparts.
Bushing
A bushing, also known as a plain bearing, is a type of bearing which facilitates motion by sliding rather than rolling. Bushings have an extremely high load carrying capacity but can only operate at slow speeds due to the high levels of friction generated by the large contact area.
Bushings typically have a long lifespan due to their minimalistic design so are commonly used on heavy duty applications where a bearing failure would be catastrophic. This includes power plant steam turbines, compressors and ship propellor shafts.
Cage (retainer)
The cage of the bearing is responsible for holding the rolling elements of the bearing in place and preventing them from falling out of the bearing.
A wide range of materials are available when it comes to bearing cages. This includes plastic, fiberglass, bronze and steel. Each material has different features and benefits making it suitable for different operating environments and applications.
Steel is one of the most commonly used materials for ball bearing cages as it has a high level of rigidity whilst being resistant to heat. Bronze is also common in roller bearings due to its ability to dissipate heat away from the rolling elements, helping to extend bearing life.
Cam follower
A is a type of needle roller bearing which features a thick inner and outer race. These bearings are typically used for rolling-track applications and can be mounting in the moving component or positioned in a stationary location to support something moving on top of it.
Many different configurations of cam follower are available. However, the most defining characteristic of a cam follower is how it mounts to its mating part. This could be through a stud or a yoke.
Cam followers are primarily designed to support radial loads although some varieties may also be able to accommodate light axial thrust loads.
Clearance
Bearing clearance is the amount of space between the rolling elements and the races of a bearing. In most cases, a bearing will require a small amount of clearance for grease or oil to be contained. However, a natural consequence of this internal clearance is a small amount of play within the bearing, or movement of the races in relation to each other.
In some cases, a bearing may require negative clearance, also known as preload. This enhances the rigidity of the bearing, preventing deformation.
Combined load
There are two types of load which a bearing can encounter: axial (thrust) load and radial load. Axial load occurs in the direction of the shaft whilst radial load is at a right angle to the shaft.
Every bearing will have different load capacities. This relates to both the magnitude of the load and the type of load. Some bearings can accommodate axial load whilst others are able to tolerate radial load.
When axial load occurs alongside radial load, this is known as a combined load. There are some bearings which are able to support both axial and radial loads simultaneously. This includes angular contact ball bearings and tapered roller bearings which are specifically designed to accommodate combined loads.
Combined loads are often found in applications such as pumps, compressors, fans, gearboxes and machine tool spindles.
Cylindrical roller bearing
Cylindrical roller bearings are designed to provide a high load carrying capacity thanks to their cylindrical-shaped rolling elements. Thanks to the large contact area of these rolling elements with the outer ring, load is distributed across a broader surface, enabling heavy radial loads to be carried.
These bearings are available in a wide range of designs, variants and sizes, making them suitable for use in many applications and industries. Sealed and split designs are also available for additional flexibility.
Cylindrical roller bearings are commonly found in electric motors, gearboxes, pumps, compressors and heavy machinery.
Fatigue
Bearing fatigue is one of the most common causes of premature bearing failure, with 34% of bearing failures attributed to fatigue.
Fatigue is most commonly caused by overloading your bearings, which causes deformation. Bearing fatigue can also be caused by heavy shock loads or high levels of vibration which cause the rings to deform.
You can help to prevent bearing fatigue by specifying a bearing which has the right load capacity for your application requirements. The early signs of bearing fatigue can often be identified through condition monitoring, allowing the bearing to be replaced before catastrophic failure occurs.
Food grade bearings
Food grade bearings are bearings which have been specifically designed for use in the food and beverage industry. This means that they are safe for using in close proximity to food and will stand up to the high-pressured washdowns which are common in the industry.
These bearings are typically manufactured from stainless steel or thermoplastics. They generally have smooth surfaces to make cleaning easy and minimise the growth of bacteria. Food grade bearings will be lubricated with food-grade lubricants which are approved for incidental contact with food items.
As well as being used on food production lines, food grade bearings are also often found in industries such as pharmaceutical and medical thanks to the high levels of corrosion resistance that these bearings deliver.
Housing
Bearing housings are used to facilitate easy mounting of a bearing to almost any surface, whilst offering the bearing some protection from harsh operating environments. Housings can be manufactured from a range of materials, although the most common are steel or cast iron.
There will be a specially machined opening within the bearing housing which contains the bearing insert. Almost any type of bearing can be housed within a bearing housing, although the most common are ball bearings and cylindrical roller bearings.
Bearing housings come in many designs including pillow blocks, flanged units and take-up units. A split-to-the-shaft design is also available to facilitate easy installation and maintenance on large diameter shafts, without the need to dismantle surrounding equipment.
Inner diameter
The inner diameter (ID) of a bearing is also known as the bore diameter. This is the measurement of the diameter inside the bearing – from one side of the inner ring to the other.
Many people attempt to measure the inner diameter of their bearings using a ruler. However, this often leads to inaccuracies. The most accurate way to measure the inner diameter of a bearing is by using a vernier caliper.
Inner ring
The inner ring of a bearing is the ring which is in direct contact with the shaft. The inner ring may have precision ground or machined raceways to guide the rolling elements.
Some bearings may not have an inner ring, with the rolling elements running directly on the shaft. This is often the case in applications where space is limited as the size of the bearing can be reduced by eliminating the need for an inner ring.
Insert bearing
A bearing insert is specifically designed for use within a bearing housing. The insert can be almost any type of bearing, although the most common bearing inserts are ball bearings or cylindrical roller bearings.
The outer race of a bearing insert is typically spherical. This allows the bearing to be inserted into the housing at a 90-degree angle and then rotated into position.
Split-to-the-shaft bearing inserts are also available for use in applications where space is limited or mounting could be challenging. Split bearings allow the bearing to be fitted without the need to dismantle surrounding equipment.
ISO
ISO stands for ‘International Organisation for Standardisation’. This is the international body which sets industry and commercial standards for everything from construction and security to quality control.
Power transmission products must meet or exceed ISO standards for a vast range of criteria including precision, tolerances, load requirements and dimensional accuracy. The majority of manufacturers base their catalogue information including load and service life on ISO-developed formulas.
Linear bearing
A linear bearing is a bearing which has been specifically designed for linear movement along a shaft or rail, rather than a radial bearing which is designed to facilitate rotational motion.
The linear bearing may be plain or it can contain rolling elements such as balls or rollers. There are many different types and arrangements of linear bearing, making them suitable for use in a wide range of applications.
Load rating
The load rating of a bearing is a number which is based on several criteria. This includes the number and size of rolling elements, the thickness of the races and a specific life calculation.
Load ratings are divided into dynamic load and static load. Dynamic load is the bearing’s load capacity during operation whilst the static load capacity is the amount of load the bearing can tolerate when it is stationary.
It’s important to look at the life expectancy of the bearing along with the load capacity. There’s no point choosing a bearing which looks like it has an impressive load capacity if it’s likely to fail quickly. The life expectancy needs to be examined in conjunction with the load capacity.
Misalignment
Bearing misalignment occurs when the faces of the inner ring and the outer ring are not parallel. This misalignment can be caused by a number of things including load, inaccuracy of the shaft and housing and mounting errors.
Some bearings are able to tolerate a certain level of misalignment but others may become damaged as a result, leading to premature bearing failure. For this reason, it’s important to consider the level of misalignment within the application before bearing selection takes place.
For applications where misalignment is unavoidable, bearings which have self-aligning capability should be chosen. This may include spherical roller bearings and self-aligning ball bearings which are able to absorb misalignment and help to prevent damage to surrounding machinery.
Needle roller bearing
Needle roller bearings are made up of long, thin cylindrical rollers which resemble needles. These rollers are typically at least four times longer than their diameter. This gives needle roller bearings an outstanding radial load capacity at moderate speeds.
Some needle roller bearings will run on an inner race, but many will run directly on a hardened steel shaft to minimise the space required. This makes these bearings ideal for use in applications where space may be limited.
Outer diameter
The outer diameter (DD) of a bearing is the measurement of the total diameter of the bearing – from one side of the outer ring to the other.
Many people attempt to measure the outer diameter of their bearings using a ruler. However, this often leads to inaccuracies. The most accurate way to measure the outer diameter of a bearing is by using a vernier caliper.
Outer ring
The outer ring of a bearing is the ring which is furthest away from the shaft, on the outside edge of the bearing. This ring will typically have precision ground or machined raceways to guide the rolling elements around the bearing.
The outer ring of a bearing is often manufactured from high-purity chrome alloy steel. This helps to deliver high load ratings and a long service life. However, other materials such as ceramics and plastics are often also available. Different materials will be more suited to different applications and operating environments.
Pillow block
A pillow block is a type of bearing unit which supports a shaft parallel to the mounting surface. If a pillow block was bolted to the table in front of you, the shaft would be horizontal.
Pillow blocks can contain almost any type of bearing including ball bearings, cylindrical roller bearings, tapered roller bearings and spherical roller bearings. These housed units offer a convenient and easy way of mounting a bearing, whilst offering some protection to the bearing in harsh environments.
Precision
The precision of a bearing refers to the tolerance to which the bearing has been manufactured. High precision bearings will have a tight tolerance, often leading to these bearings to have a higher load rating combined with a lower level of operational noise.
Bearing precision is measured using the ABEC (Annual Bearing Engineering Committee) rating system. Around 98% of bearings are manufactured to ABEC 1 or ABEC 3 standards, whilst is perfectly sufficient for most applications including automotive, electric motors and gearboxes.
However, some applications require high levels of precision, such as aerospace, machine tools and medical devices. These applications demand ABEC 5, ABEC 7 and even ABEC 9 rated bearings, the highest possible level of precision.
The level of precision required will depend on the application that the bearing is being used in and requires careful consideration.
Preload
Bearing preload is also known as negative internal clearance. The process of creating bearing preload involves adding a sustained axial load to the bearing, ensuring constant contact between the rolling elements and the races.
The most common reason that preload is added to a bearing is to increase the level of rigidity in high-precision applications. Preload can also help to reduce noise levels during operation, improve running accuracy and prevent skidding in high-speed applications.
Raceway
The bearing raceway is the track on which the rolling elements of a bearing run. The raceway of a bearing is typically situated on its inner or outer ring, although some bearings used a hardened shaft as a raceway to save space.
In most ball bearings, the raceway takes the form of a small groove in the raceway where the balls run. The raceway guides the balls around the bearing, preventing them from slipping out of the bearing during operation.
Radial load
Most bearings are designed to carry radial load. This is load which is applied at a 90-degree angle to the shaft. This type of load is common in material handling, steel mills and conveyor applications.
Bearings such as cylindrical roller bearings, needle roller bearings and deep groove ball bearings can typically accommodate radial load, although the magnitude of load they can carry will depend on the type of bearing.
When radial load occurs alongside axial load, this is known as combined load. Bearings such as angular contact ball bearings and tapered roller bearings are designed to accommodate combined loads.
Roller bearing
A roller bearing, also known as a rolling-element bearing, is made up of several rollers which are typically held together by a cage or retainer between an inner ring and an outer ring.
There are many different types of roller bearing which are defined by the types of rolling elements. The rollers within a roller bearing can be cylindrical, needle, tapered or spherical. Each type of roller bearing has different features and benefits making it appropriate for certain applications.
For example, cylindrical roller bearings have a high load carrying capacity but generally can’t tolerate axial thrust loads. Needle roller bearings are ideal for high load capacities where space is limited. Spherical roller bearings have a high load carrying capacity with self-aligning capabilities. Tapered roller bearings are often found in vehicle wheels thanks to their ability to accommodate combined loads.
Rolling elements
The rolling elements of a bearing are situated between the bearing’s inner and outer rings and are used to transmit rotational motion whilst minimising the coefficient of friction.
There are many different types of rolling element available, each with different properties and benefits. The type of rolling element that you’ll choose will depend on your application requirements including load, speed and operating conditions.
Rolling elements are divided into balls and rollers. Generally speaking, ball bearings are typically used for high-speed applications with low to moderate load requirements, whilst roller bearings are preferred for applications with heavy load requirements operating at moderate speeds. However, there are many variations of each type of bearing, with options available to suit every application requirement.
Seal
A bearing seal is designed to keep the lubricant within the bearing and prevent the ingress of contamination. Seals are highly effective at protecting the bearing is the right sealing solution is chosen and fitted and maintained correctly.
Bearing seals are typically fixed to the outer race, with moderate contact with the inner race. This causes a small amount of friction which is generally not noticed in slow moving applications. However, in high-speed applications, this can sometimes cause heat to be generated. Some manufacturers have designed contact-free seals for use in high-speed applications.
Self-aligning bearing
Self-aligning bearings are designed to compensate for misalignment, protecting surrounding equipment from damage whilst extending the life of the bearing. These bearings are recommended when the alignment of the shaft and housing is difficult or where the shaft may bend during operation.
Shield
For applications where contact seals are not appropriate due to high-speed operation, bearing shields may be used to protect the bearing. Metal shields are designed to prevent larger particles from entering the bearing whilst reducing lubricant leakage.
Shields may be pressed into the outer ring of the bearing (non-removable bearing shields) or retained using a circlip (removable bearing shields).
As bearing shields do not make contact with the inner ring of the bearing, the don’t increase starting or running torque and don’t contribute towards friction or heat generation. However, since there’s space between the shield and the inner race, small contaminants may be able to enter the bearing.
Spherical roller bearing (SRB)
Spherical roller bearings, often abbreviated to SRB, are made up by several spherical rollers which are held together with a cage or retainer between the bearing’s inner and outer ring. These bearings are able to accommodate both radial and axial thrust loads at high speeds.
Invented by SKF back in 1919, these bearings are suitable for use in applications which are prone to misalignment and shaft deflections thanks to the innovative shape of the rolling elements.
Spherical roller bearings can often be found on the main shafts of wind turbines as well as in the mining and quarrying, metals and marine industries.
Split bearing
Split bearings feature a separable design to make mounting and maintenance quick and simple in even the heaviest of machinery and the most inaccessible of locations. This helps to reduce downtime and improve worker safety.
A wide range of roller bearings are available in a split design, including split spherical roller bearings, split cylindrical roller bearings and split tapered roller bearings.
Split bearings can also be mounted within a split housing to offer the bearing protection from the operating conditions and to facilitate easy mounting.
Tapered roller bearing
Tapered roller bearings are most commonly found in the wheels of cars, lorries and trailers. These bearings are made up of several tapered rollers, held together with a cage or retainer between two bearing rings.
The rollers and cage of a tapered roller bearing are typically assembled to the inner race and are known collectively as the cone of the bearing. The outer race is generally separate and is known as the cup of the bearing.
These bearings can tolerate both radial and axial thrust loads and are available in both single and double row varieties for additional load carrying capacity.
Thrust bearing
Thrust bearings are designed to accommodate axial thrust loads. A wide variety of rolling elements can be found within a thrust bearing including balls, needle rollers, cylindrical rollers and tapered rollers.
The rolling elements are typically held together using a cage or retainer and sandwiched between two thrust washers.
Thrust bearings are used wherever the load is transmitted along the length of a shaft rather than against it. This includes aerospace, marine and automotive applications.
Tolerance
Tolerance refers to the margin of error that a bearing is manufactured to when it comes to dimensions. A bearing manufactured to a wide tolerance will have moderate levels of precision, whilst a bearing manufactured to tight tolerances will have high levels of precision.
The precision of a bearing is measured using the ABEC (Annual Bearing Engineering Committee) rating system which includes the numbers 1, 3, 5, 7 and 9. A bearing with a rating of ABEC 1 will have wide tolerances whilst a bearing rated as ABEC 9 is manufactured to tight tolerances.