Do you feel chained to your lubrication schedule?
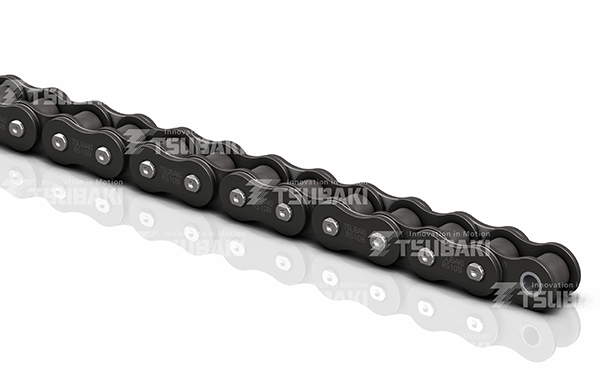
Lubrication is an important aspect of any moving component. It reduces friction and wear between parts, as well as helping to seal against contamination. However, that doesn’t mean it can’t feel like a chore sometimes, especially if the parts needing lubrication are difficult to access.
Roller chain is no different. For chain to have the best chance of achieving its maximum possible service life, optimal lubrication is key. The lubrication forms a slippery film over the moving components, reducing direct metal-on-metal contact in order to minimise friction and wear.
The lubrication also acts as a barrier to protect the metal components of the chain from corrosion, as well as providing a buffer against the impact of sprocket-roller engagement, reducing noise levels and enabling smoother operation.
However, roller chain lubrication isn’t always as easy as it may sound.
Inaccessibility of the drive can make relubrication a challenge, leading to excessive downtime, inflated costs and an increased risk of worker injury. This sometimes results in lubrication intervals being extended beyond the manufacturer’s guidelines, with excessive lubricant being applied in an attempt to counteract these extended intervals.
Manual relubrication also enables the possibility for human error. Using the wrong quantity or type of lubricant can be extremely detrimental to the service life of the roller chain. There is also the risk that contaminated lubricant may be applied to the chain, introducing contamination to exposed components.
Thankfully, Tsubaki has developed the cutting-edge Lambda chain, which requires no relubrication over its lifespan, as well as dramatically increasing service life.
Tsubaki’s Lambda chain has oil-impregnated bushes, which supply lubricant directly to the areas that need it the most, throughout the chain’s entire service life. This removes the need for manual relubrication, reducing downtime and removing the possibility of lubrication errors.
This chain is supplied with food-grade NSF-H1 grease as standard, making it ideal for use in the food and beverage industry, as well as in pharmaceutical applications. H3 certified lubricant is also available upon request, for use in applications where contact with food products is unavoidable.
Many chains which are manually lubricated feel wet or sticky to touch. This leads to the build-up of contamination on the chain and increases the frequency that cleaning is required to keep the chain operational. Lambda chain is dry to touch, thanks to the oil-impregnated bushes, meaning that contamination on the chain is greatly reduced. This reduces maintenance requirements and helps to extend the service life of the chain.
Tsubaki’s Lambda chain is available in both single and double strand variations, in both British and American Standard. High-temperature, corrosion-resistant and extra strength Lambda chains are also available.
For more information about Tsubaki’s maintenance-free Lambda chain, contact your knowledgeable local sales team today.