How Does a Linear Actuator Work?
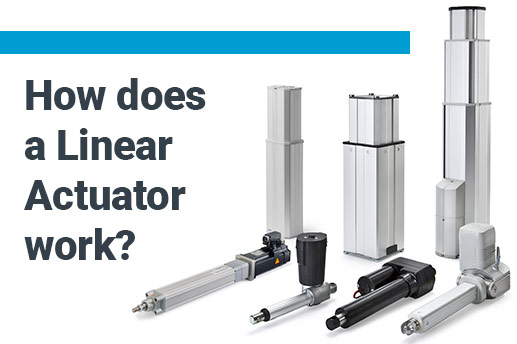
One of the most common questions that we get asked here at ACORN® is ‘how does a linear actuator work?’. Understanding how an actuator works can help you to make an educated decision when it comes to selecting a linear actuator for your application, so there’s no wonder that so many people ask this question.
Linear motion involves some highly complex concepts, so many explanations that you’ll find online can be difficult to understand. We’re here to make linear straightforward for you. In this article, we’ll explain exactly how a linear actuator works, as well as some of the terminology that you might see used to describe them.
What is a linear actuator?
A linear actuator (opens new window) is a machine component that is designed to convert rotational motion from an electric motor into linear motion. These components are typically used for straight push / pull movements, although they can also be used for lifting and tilting.
When we talk about linear actuators, we often discuss the trade-off between force and speed. However, to fully appreciate this, it’s useful to understand how a linear actuator works, and what is going on inside the actuator during operation.
Types of linear actuator
There are two main types of linear actuator that you need to be aware of: positioning linear actuators and thrust force electric linear actuators. Whilst these two types of actuators are similar in some ways, there are differences between the two, meaning that each has its own unique set of features and benefits.
Let’s look at what’s inside each of these types of linear actuators, as well as how each type creates linear motion.
What’s inside electric linear actuators?
Perhaps the most common form of actuator is the thrust force electric linear actuator.
The illustration below, courtesy of Ewellix shows the typical construction of an electric linear actuator.
1. Front attachment
2. Inner tube or Push tube
3. Screw
4. Nut
5. Electrial motor
6. Gearbox
7. Electrical cable
8. Rear attachment
9. Outer tube or protection tube
10. Sealing system
The actuator itself consists of a tube that sits on top of a lead screw, ball screw or, in some cases a roller screw. This tube is what creates push/pull force and movement.
Some linear actuators will also contain limit switches, which are used to control the stroke of the actuator.
How do electric linear actuators work?
So, now you know what is inside the linear actuator, but how do all of these parts interact together to create smooth and accurate linear motion?
The purpose of an electric linear actuator is to convert the rotary motion of an AC or a DC motor into linear motion, providing the force necessary to move and position an object or a piece of equipment. This might sound simple enough in principle, but linear actuators use various technologies to fulfil this role in the smoothest and most accurate way possible.
When power is applied to the linear actuator the electric motor begins to rotate, which drives the internal gearbox.
The rotational force (torque) is transferred via the gearbox to the screw, causing rotation. This is where the rotational motion is transformed into linear motion, as the rotation of the screw drives the rod which begins to move.
Many push/pull electric linear actuators have varying force and speed characteristics within the same model range. Why is this? As the motor stays a constant (thus the maximum available torque is a constant), then changes in the gearbox provide the facility for different movement characteristics dependent on the application. Commonly, this is the trade-off between speed and force; higher force but lower speed, or higher speed with lower force.
The rod extends until the power is cut. The power cut off signal often comes from a limit switch, which cuts the power when the rod reaches a certain point. The polarity is then reversed, causing the rod to retract until it again receives a signal to stop. Control of movement can also be from external devices.
How does a mechanical positioning linear actuator work?
This type of actuator is primarily used for the accurate positioning and smooth, controlled movement of an object, or sub system, within a larger machine.
Traditionally, this has been achieved using a pair or parallel profile rail guide assemblies (or roller guides), mounted on a suitable surface, with a table mounted to the carriages on each rail upon which the object or system is secured. Drive is often provided by a ball screw, which must be properly and accurately mounted to the system. Belts are also used, particularly for long strokes. The profile rail guides also need to be set up within a tight tolerance for parallelism and height. As you can imagine, this can be a time consuming, hence costly, procedure. This is where positioning linear actuators come in.
The linear actuator combines guidance, drive and mounting interface all within the same unit. Each actuator will have its own capabilities with respect to positioning accuracy, speed, stroke, etc. Thus, it is possible to specify a complete movement solution in a single component. In this way installation time and complexity is greatly reduced and concerns on system performance are eliminated.
Drive usually comes from an electric motor, often a servo type, but DC and AC motors are also used. Linear actuators can be supplied complete with motor and gearbox but are usually specified without these components. This is to allow the user/designer to select the optimum motor, gearbox, controller, etc. for their application.
The conversion of rotational torque to translational (linear) movement is often by means of a ball screw. However, belts are also very common, as these allow for far greater strokes (10m + strokes are available) along with cost savings.
The below illustration of a Nadella linear actuator clearly shows the guidance (rollers in this instance) along with the drive (toothed) belt and mounting plate.
For applications where very high levels of accuracy and running performance are required, linear actuators often use rigid channels for guidance. This can also allow for simple supporting of the actuator. The below illustration of a THK actuator clearly shows the component parts of this actuator:
How are linear actuators controlled?
So, now you know how linear actuators work, but how are linear actuators controlled?
This is another question with an answer that is dependent on the type of actuator and its setup. That’s because different actuators can be controlled in different ways. This means that the exact control method for an actuator is dependent on the type of electric motor that is used and the characteristic of the actuator itself. Control can be as simple as a motor, power supply and switch. More commonly, control will involve a servo, ‘smart’ or other motor, with the associated drive, controller, etc. Often actuators are used within larger machine systems and are controlled by the machine PLC. Some actuators are independent systems, but still require some interfacing with a PLC. Other actuators are capable of complex movement profiles that can be simply programmed via PC software, rather than from a PLC.
Where are linear actuators used?
Linear actuators are used across a wide variety of different industries. Wherever something needs to be lifted, lowered, pushed, pulled or positioned, linear motion technology leads the way.
Some of the industries in which you’ll find linear actuators include:
-
Aerospace
-
Automation
-
Automotive
-
Energy
-
Food and beverage
-
Machine tool
-
Materials handling
-
Medical
-
Packaging
-
Pharmaceutical
-
Printing
In summary
Linear actuators are a popular machine component which enable rotational motion to be transformed into smooth and accurate linear motion. This facilitates the precise positioning of components, as well as lifting, lowering, pushing and pulling motions. That’s why linear is such a popular technology across almost every industry.
In this article, we’ve explained how linear actuators work, as well as where they are used in industry. If you’re looking for the right linear actuator for your application, or if you want to find out more about how linear actuators work, our linear motion specialists are on hand to help. Give them a call today for expert support and assistance. (opens new window)