Top causes of premature roller chain wear
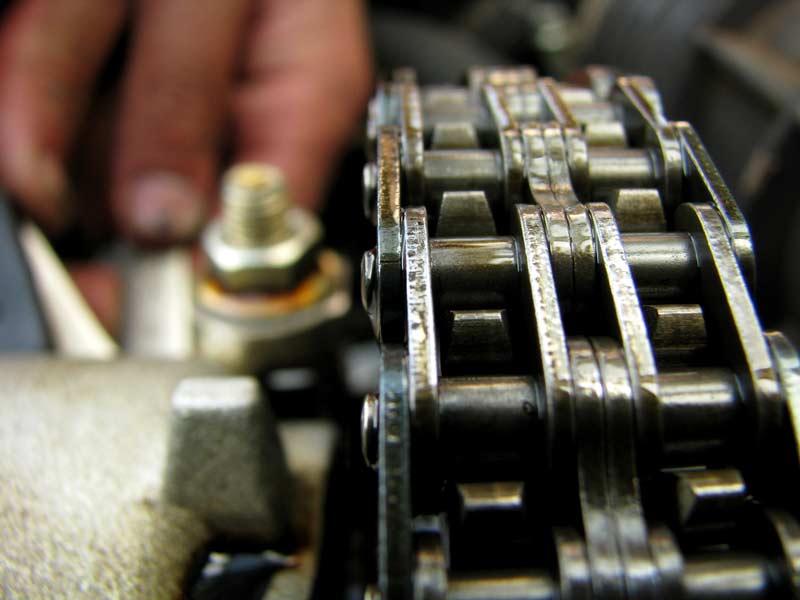
Roller chain is one of the most commonly used industrial components, found across the industries: from mining & quarrying to marine, and food & beverage to pharmaceuticals. Roller chain has two main purposes, which are to transmit power, and to convey materials. As a large proportion of industrial applications are dependent on roller chain, it is critical to prevent premature wear in order to extend the lifespan of the chain and to prevent unplanned downtime and unnecessary costs.
Every roller chain will have an expected service life, according to the specification of the chain and the conditions of usage. Even the highest quality chains, used exactly according to the manufacturer specifications, will slowly wear. It is premature wearing that has the biggest impact on businesses.
Roller chain is made up of a series of connected bearings, which articulate as they enter and leave the sprockets. Every engagement with the sprocket causes wear on the pins and bushings. As material is worn away from these surfaces, the roller chain will gradually elongate.
One of the most common countermeasures put in place to reduce chain wear is lubrication. Lubrication systems are installed in an attempt to prevent wear, or to at least delay it to give the chain the best chance of achieving its maximum service life.
The chosen lubrication type and method for a roller chain drive needs to be based on the drive’s specifications. An optimum lubrication system will help to reduce wear, as well as cushioning impact loads and assisting with heat dissipation, which in turn can also help to prevent premature wearing in the roller chain drive.
No matter how much care is taken in selecting the correct lubrication system, this could be compromised by contamination. Contamination by dirt, rusting or exposure to corrosive environments may prevent the lubricant from penetrating pins, rendering the well thought out lubrication system useless. The correct chain and lubrication system should be selected based on the operating environment, as well as the operating environment being kept as free from contaminants as possible, in order to prevent premature wearing of the chain.
Misalignment of both the shafts and sprockets has the potential to cause premature chain wear, by causing uneven loading across the chain width. These types of misalignment can lead to roller linkplate and sprocket tooth wear. The use of a simple straight edge, or a more sophisticated and accurate laser alignment tool such as those available from SKF can help to ensure that both sprockets and shafts are aligned and reduce the chance of premature chain wear.
Excessive loads which exceed the chain’s dynamic load bearing capacity are a common cause of premature chain wear. This can occur in the form of both cyclic and shock overloading. Excessive cyclic loading can lead to cracked inner link plates, whilst extreme shock loads may cause pins to bend, twist or break. Care must be taken to ensure that the right chain product is selected for the predicted application load, and that loads experienced in operation do not exceed the manufacturer’s specifications for the product.
In conclusion, it is essential to begin the application design process by selecting a quality chain, with specifications to meet the application requirements. Lubrication, contamination, misalignment and loading should be checked at regular intervals to ensure that the chain is being cared for effectively, in order to reduce the chances of premature chain wear and enable the chain to achieve its best possible service life.