Top 5 Reasons for Premature Bearing Failure
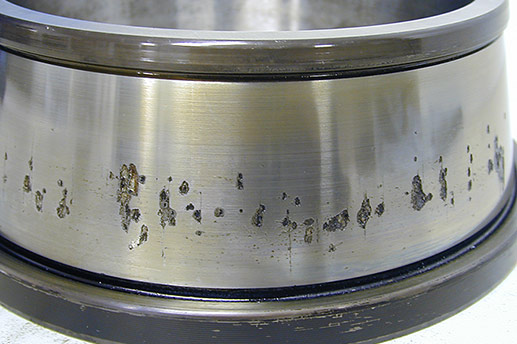
From unplanned downtime to catastrophic machine failure, the costs of premature bearing failure can be high. Understanding the most common causes of bearing failure can help you to avoid bearing damage, reducing both downtime and costs to the business.
Below, we go through the top 5 reasons for premature bearing failure, as well as how to prevent them.
1. Fatigue
What It Is
The most common cause of bearing failure is fatigue, with 34% of all premature bearing failures being attributed to fatigue. This could be that the bearing is at its natural lifecycle end, but it can also be caused by using the wrong bearing for the application.
How To Prevent It
There are many requirements which need to be considered when selecting a bearing, including load (weight and type), speed, and misalignment. There is no bearing that is suitable for every application, so each case needs to be considered individually, and the most appropriate bearing selected.
2. Lubrication Problems
What It Is
Lubrication problems account for a third of premature bearing failures. This can be caused by too little, too much, or the wrong type of lubrication. As bearings are often the most inaccessible component in an application, the required re-lubrication intervals are often not met, causing the bearing to fail prematurely.
How To Prevent It
There are two solutions to this. Maintenance-free bearings such as SKF Explorer Sealed bearings, or RHP Self-Lube bearings can be used, which require no re-lubrication throughout their service life. Another option would be to fit an automatic lubrication system, such as the System 24 range from SKF. This takes the manual effort out of re-lubrication, and ensures that the exact quantity of lubrication is dispensed at the exact interval.
3. Incorrect Mounting
What It Is
Around 16% of all premature bearing failures are caused by incorrect mounting. There are three types of fitting: mechanical, heat and oil. If the bearing is not fitted correctly, it can become damaged either during or as a result of the fitting process, and hence fail prematurely.
How To Prevent It
The use of oil baths or naked flame is not recommended, as it causes contamination, and it is very difficult to ensure a consistent temperature, which could lead to bearing damage.
Mechanical fitting is often used, and if done correctly, can be a safe way of mounting a bearing. A bearing fitting tool kit should be used, such as the SKF TMFT 36, to ensure that even force is applied across the bearing to avoid damage.
Heat is a very effective method of mounting a bearing, but the maximum operating temperature of the bearing must be taken into consideration, to ensure that the bearing is not overheated. One of the safest way to do this is by using a bearing heater, such as the SKF TIH range. This will ensure that the bearing is heated to the optimum temperature, without overheating and causing damage to the bearing.
4. Improper Handling
What It Is
Improper storage and handling exposes bearings to contaminants such as dampness and dust. Improper handling can also cause damage to the bearing, by scratches and indentation. This can render the bearing unusable, or cause the bearing to fail prematurely.
How To Prevent It
Always follow the manufacturer’s storage instructions, and ensure that the bearing is only handled when necessary to ensure that your bearing is given the best possible chance of achieving its expected service life.
5. Contamination
What It Is
Contamination can result from improper storage or handling, but it can also be caused by insufficient protection. This could be using the incorrect seal for the application or temperature ranges, or due to misalignment. Seals are only able to take up to 0.5o of misalignment. If the seal does not fit exactly right, this could lead to contaminants entering the bearing, hence reducing service life.
How To Prevent It
Ensure that you are using the right seal, shield or grease for your bearing, as well as for the conditions. If you heat the bearing for fitting, consider how this may affect the seal. Also consider how misalignment and how this may affect the protection used. Even the most suitable bearing for the application will fail if the seal is not right.
If any one of these factors is weak, bearing service life can be compromised. In order to achieve maximum bearing service life, we need to ensure that all of these factors are taken into consideration, and that the most suitable bearing, lubrication, mounting technique, storage and handling practices and seals are chosen for the individual application requirements.